DRB Holding Co., Ltd. Main menu
All Menu
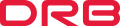
DRB establishes Safety First management policy and exerts itself for safe management in all business places. At the same time, DRB promotes various policies to create safe workplaces and improve the satisfaction level of all employees.
DRB has sought to eliminate internal safety risk factors while simultaneously executing health and safety activities for DRB's external suppliers. We will continue to work with external providers to strengthen our health and safety management skills. Furthermore, we will address risk issues identified during on-site assessments and execute changes and investments through external supplier safety management reviews. DRB Industrial and DRB Automotive hire specialized agencies to examine the degree of exposure to physical and chemical risks such as chemicals and noise in the workplace. Measurement results are posted on the work bulletin board or communicated to employees through regular health and safety training sessions. In addition, DRB Industrial prevents possible accidents by replacing outdated high-voltage switchboards for stable power supply at the workplace and efficient management of power facilities, and it minimizes damage from accidents by preparing measures to respond quickly in the event of an accident. In addition, we plan to establish a web-based smart power monitoring system to computerize power- related data and increase the efficiency of power distribution and management through the response to power demand (peak) based on statistical analysis. DRB Automotive has installed an automatic CO2 extinguishing system for the extrusion vulcanization process within its mass production plant. For the coating process, a manual CO2 fire extinguishing device is equipped to enable effective early extinguishing in the event of a fire. By means of these initiatives., DRB is averting serious accidents such as burns from massive flames and suffocation from poisonous fumes.
To increase the safety management capability and system quality in all business places up to the global level, DRB is building a safety management system in both mid- and long-terms. Also, by assessing the safety system and safety culture level in the workplaces, we are planning to find out various risk factors and weakness and improve them in a fundamental manner.
DRB improves the safety of facilities in operation by conducting risk assessments and removes root causes of risk factors through inspections. DRB Industrial and DRB Automotive perform risk assessments involving all department personnel at least once a year. For safety management, required changes discovered through risk assessment are implemented horizontally to all departments. Moreover, when new equipment and facilities are introduced or risk assessment requirements change as a result of legislation or amendments to health and safety-related laws and regulations, irregular assessments are conducted. Factors identified as having a risk level of 4 or higher, based on the results of the risk assessment, are recorded in the important risk register. Immediate improvement or risk reduction measures are then established, with plans prioritized based on the level of risk in order to address these factors. Furthermore, these risk mitigation measures are incorporated into the relevant annual business plan and work promotion plan to reduce or eliminate the identified risks. DRB identified hazardous risk factors for each process, developed a plan to determine and reduce risks, and then conducted a risk assessment involving workers from all departments at each domestic business site to prevent safety accidents. We monitored the improvements identified during the assessment and carried out safety management actions through horizontal deployment after applying the assessment findings of certain departments to all departments. DRB intends to undertake safety diagnosis and semi-annual risk assessments in order to continually improve possible risk factors.
DRB strives to improve the level of safety and health of our affiliates and to realize mutual growth in this area.
DRB takes an immediate measure to respond to any emergency situation based on its emergency response system. Also, to improve the emergency response capability of the members, both executives and staffs, we provide emergency response training and education every year based on the type of disaster scenarios, such as industrial accident, fire, environmental accident, or natural disasters.
DRB believes that its competitiveness depends on its employees’ health, and therefore carries out various health improvement activities, such as non-smoking campaign, safe drinking campaign, fitness activity, low salt diet, No Stress campaign, and customized health examination. In addition, we operate a health care office and health programs focusing on musculoskeletal system, obesity, and non-smoking efforts. As a mental health program, we provide a professional counseling service, “Sandgam4U” and try to help our members release and reduce work-related stress.
DRB provides all employees with safety equipment and garments in accordance with the protective equipment use and management regulations, and makes sure the members’ compliance with the regulations. In detail, we instruct and guide them to wear mandatory protective equipment in each process and work area, such as safety helmet, gas mask, dust mask, earplugs, ear caps, face shield, protective goggles and gloves.
DRB has formal processes in place, such as manuals, procedures, and guidelines covering the purchase and handling of chemicals, screening, and management of employees with health issues. In the event of an addition or change of chemical substances, the health and safety manager records the information in the complete chemical substance enumeration, an internal management document. The enumeration includes the findings of a review of substances subject to statutory regulations regarding health and safety, and it serves as a basis for the placement of the MSDS in the workplace or the attachment of hazard warning signs. Furthermore, DRB categorizes the hazardous compounds handled by personnel and measurement substances in the workplace for each process and provides this information to measurement and inspection organizations.
DRB develops health and safety policies, continually trains all employees to follow them, and operates an emergency response system to guarantee that swift action is taken in the case of an accident. Moreover, we perform emergency preparedness training and education based on scenarios for various types of disasters, such as various safety accidents, fires, environmental accidents, and natural disasters, in order to increase our employees' emergency response capabilities. In addition, personalized training is offered to internal employees by class and job function to help them build their safety competencies. In particular, for those in charge of chemical handling, we provide pre-training on the Material Safety Data Sheet (MSDS), which includes information on the hazards and risks of chemicals handled by workers. Furthermore, DRB Industrial and DRB Automotive offer statutory safety training to their workers and those from external suppliers each year in order to enhance their safety awareness and reduce safety risks. At the same time, both companies provide separate training on handling hazardous substances to workers of external suppliers.
좌우로 스크롤 하시면
내용이 보입니다.
Company | Education | Target | Training period(hours) |
---|---|---|---|
DRB Industrial | Safety training on hazardous chemicals | Hazardous chemical managers and handlers | 2023.5.9~10.26(16 hours/2 years) |
Emergency (fire) response training | Production workers | 2023.4.28(1/2 hours) | |
External training for supervising managers | Supervising manager | 2023.4.12~12.7(16 hours) | |
Risk assessment personnel training | Supervising manager | 2023.4.24~10.12(16 hours) | |
Regular health and safety training | All employees | 2023.1~12(12 hours/semi-annual) | |
DRB Automotive | Emergency response training in case of accidents | Supervising manager, Production workers | 2023.11.20/27/30(2 hours) |
Emergency (fire) response training | Production workers | 2023.10.23/30(2 hours) | |
External training for supervising managers | Supervising manager | 2023.1.2~2023.12.19(16 hours) | |
DRB Qingdao | Occupational health training | Production workers | 2023.7.15(4 hours) |
Emergency rescue training | Production workers | 2023.9.8(4 hours) | |
Occupational health manager training | Occupational hygiene manager and staff | 2023.10.16(8 Hours) | |
Safety training on return to work | Production workers | 2024.2.3(4 hours) | |
Safety training on hazardous work | Production workers | 2024.5.30(4 hours) | |
DRB Vietnam | ISO 45001:2018 internal audit training | ISO45001:2018 internal auditor | 2023.3.1~3.3(24 hours) |
DRB makes various efforts to keep its workplace environments, internal and external, clean and safe for all workers and to maintain their health with hygienic practices. To solve the inconvenience in using safety and protective equipment in the field, we collaborate with protective equipment manufacturers to improve the convenience and function of the protection gears, and also carry out “hearing protection program” for the workplaces that are vulnerable to noise. In addition, for working areas with low oxygen density, we not only prepare and comply with the safety and health standards, including ‘healthy working program for workers in confined space’, but also establish and implement the Material Safety Data Sheet (MSDS) system in accordance with the Globally Harmonized System of Classification and Labeling of Chemicals (GHS) standards, strictly, for proper use of chemical substances.
DRB is seeking to provide a health-friendly work culture and environment. We will evolve into an exemplary company that continuously strives to practice health- conscious management by fostering a healthy organizational culture and work environment while helping our employees manage their own health.
좌우로 스크롤 하시면
내용이 보입니다.
Health checkup |
|
|
---|---|---|
Health management |
|
|
Sleep health promotion program |
|
|
Customized exercise education program |
|
|
Anti-smoking program |
|
|
Mental health promotion program |
|
|
ICT-based mobile healthcare |
|